Multi-axis machining represents a significant leap in precision manufacturing, enhancing manufacturing accuracy and opening new possibilities for producing complex geometries previously unattainable with traditional methods. This advanced technology allows cutting tools to move along multiple axes, enabling the creation of intricate and precise parts. Continue reading this article as we uncover the fundamentals of multi-axis machining and the significance of each axis. We will also examine its diverse applications and discuss its advantages and disadvantages.
What Does Axis Stand For in Machining?
In machining, the term “axis” refers to the direction the cutting tool or workpiece can move. Traditional machining typically involves three primary axes: X, Y, and Z. The X-axis represents left-to-right movements, the Y-axis covers front-to-back movements, and the Z-axis deals with up-and-down movements. Each axis is vital in defining the tool’s position and movement, contributing to the precision and complexity of the machined part.
As a result, understanding the concept of axes is fundamental to grasping the capabilities and advancements offered by multi-axis machining. Moving beyond the primary three axes, multi-axis machining introduces additional degrees of freedom, enabling more intricate and detailed manufacturing processes.
What Is Multi-Axis Machining?
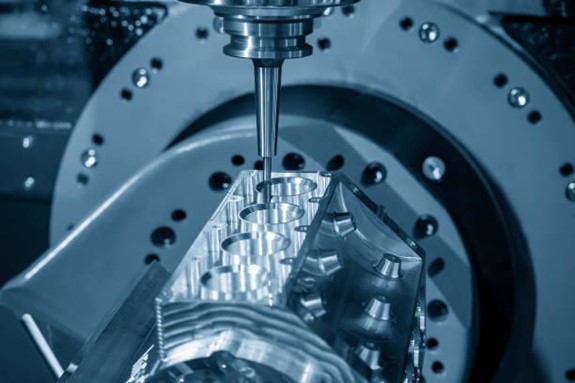
5-axis CNC milling machine operating on an aluminum engine part
Multi-axis machining refers to a manufacturing process where the cutting tool can move along multiple axes simultaneously to create complex and precise parts. Unlike traditional three-axis machining, which operates along the X, Y, and Z axes, multi-axis machining introduces additional rotational axes, such as the A, B, and C axes.
These rotational axes allow the cutting tool or workpiece to rotate around the X, Y, and Z axes. For instance, the A-axis rotates around the X-axis, the B-axis rotates around the Y-axis, and the C-axis rotates around the Z-axis. This capability allows for even more intricate designs and reduces the need for multiple setups.
Multi-axis machining can be categorized into several types based on the number of axes involved:
4-Axis Machining
In addition to the standard X, Y, and Z axes, a fourth axis (typically the A-axis) allows rotation around the X-axis. This additional axis can machine complex contours and angles that would prove difficult with a three-axis setup. 4-axis machining is particularly useful for tasks such as engraving, cutting holes on the sides of a part, and creating intricate patterns on cylindrical objects.
5-Axis Machining
This advanced type incorporates two additional rotational axes, usually the A and B axes. 5-axis machining enables the production of highly complex parts with fewer setups and manual interventions. Rotating the cutting tool or the workpiece in two directions allows for machining intricate geometries, such as turbine blades, impellers, and medical implants.
6-Axis Machining and Beyond
While less common, some specialized applications require six or more axes, providing even more degrees of flexibility and precision. 6-axis machines add a rotational axis, such as the C-axis, which rotates around the Z-axis. This capability remains essential for highly complex parts that demand extreme precision and intricate detailing. Industries like aerospace utilize these advanced machines to create components with tight tolerances and complex shapes.
Applications of Multi-Axis Machining
Multi-axis machining has a broad range of applications across various industries due to its ability to produce complex and precise parts efficiently. By enabling the cutting tool to move along multiple axes, this technology meets the demanding requirements of modern manufacturing.
Below are some of the critical applications of multi-axis machining:
Aerospace Industry
The aerospace sector requires parts with extremely tight tolerances and complex geometries. Multi-axis machining is crucial for producing turbine blades, aircraft structural parts, and engine components. The ability to machine intricate shapes and fine details ensures the optimal performance of aerospace components.
Automotive Industry
Multi-axis machining is used in the automotive industry to fabricate engine parts, transmission components, and intricate body parts. The precision of multi-axis machining helps produce these components to meet stringent industry standards.
Medical Device Manufacturing
The medical field demands highly precise components, often with unique shapes and fine details. As such, multi-axis machining remains ideal for creating medical implants, prosthetics, and surgical instruments. Its ability to machine complex geometries ensures that these components meet the specifications required for medical applications.
Energy Sector
Multi-axis machining also applies in producing components for wind turbines, oil and gas equipment, and nuclear reactors. The technology enables the creation of parts with complex shapes and precise tolerances, essential for the efficiency and safety of energy production systems.
Consumer Electronics
The consumer electronics industry benefits from multi-axis machining in producing small, detailed components such as casings, connectors, and circuit board parts. The technology’s precision and ability to handle a variety of materials make it ideal for manufacturing components that meet the high standards of consumer electronics.
Custom Manufacturing
Beyond these specific industries, multi-axis machining is valuable for custom manufacturing projects that require unique, one-off parts. The ability to machine complex shapes and fine details makes it ideal for prototyping and producing custom components for various applications.
Pros and Cons of Multi-Axis Machining
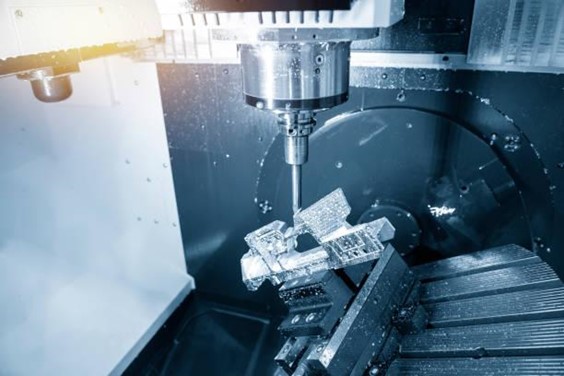
a multi-axis machine cutting an aerospace component
Multi-axis machining offers numerous advantages, making it a preferred choice in various industries. However, it also comes with some drawbacks that need consideration. Thus, it’s best to understand this technology’s pros and cons to make informed decisions in manufacturing processes.
Pros of Multi-Axis Machining
Here are the benefits of multi-axis machining:
Enhanced Precision and Accuracy
Multi-axis machining allows for the creation of intricate and complex parts with high precision. Besides, the capability to machine parts with complex geometries, undercuts, and intricate features sets multi-axis machining apart from conventional methods. This level of precision is particularly beneficial for high-stake industries like aerospace.
Reduced Setup Time
Multi-axis machining significantly reduces the need to reposition the workpieces by enabling multiple operations in a single setup. This saves time and minimizes the potential for errors, leading to higher efficiency and consistency in the manufacturing process. Furthermore, reducing setup time contributes to lower overall production costs and faster turnaround times for projects.
Improved Surface Finish
The technology’s ability to approach the workpiece from various angles results in a superior surface finish. This is particularly beneficial for parts that require a high-quality finish, as it reduces the need for additional finishing processes. A better surface finish improves the aesthetic appeal of the part and enhances its functional properties, such as wear resistance and fatigue strength.
Greater Flexibility
Multi-axis machining handles various material grades, including metals, plastics, composites, and ceramics. This versatility makes it suitable for diverse applications across different industries.
Cons of Multi-Axis Machining
Below are the limitations of multi-axis machining:
High Cost
The initial investment in multi-axis machining equipment is often substantial for most startups. These machines are way more expensive than three-axis machines, and maintenance and operation costs stand on the high side. Besides, the advanced software required for multi-axis machining adds to the overall cost. So, manufacturing companies must consider the long-term benefits and potential return on investment when investing in multi-axis technology.
Software Dependence
The reliance on advanced software for programming and control means that any issues with the software can impact the machining process. Consequently, manufacturers must ensure the software is up-to-date and compatible with the equipment. Further, software updates and troubleshooting can require specialized knowledge and support. This, in turn, contributes to the overall complexity of managing multi-axis machining operations.
Increased Setup Complexity
While multi-axis machining reduces the need for multiple setups, the initial setup can be more complex and time-consuming. Proper alignment and calibration are essential to achieve the desired precision and accuracy. This complexity poses a barrier for small-scale manufacturers who may need more resources or expertise to handle advanced setups.
Complex Programming
Multi-axis machining requires advanced programming skills and knowledge of sophisticated software. This can lead to a steeper learning curve and the need for specialized training for operators and programmers. Furthermore, programming complexity can result in longer setup times for new projects and increased potential for programming errors.
Conclusion
Multi-axis machining has revolutionized modern manufacturing by offering enhanced precision, reduced setup time, and greater flexibility. Its ability to handle complex geometries and a wide range of materials makes it indispensable across various industries, including aerospace, automotive, medical device manufacturing, and more.
Despite the higher costs and complexity associated with its programming and setup, the benefits often outweigh these challenges, making it a valuable investment for many manufacturers. By understanding the pros and cons of multi-axis machining, companies can make informed decisions to leverage this advanced technology effectively, ultimately improving their production capabilities and product quality.